Latest News
The latest and greatest project news
Repairing vs. Replacing Hydraulic Cylinders

Hydraulic cylinders play an essential role in numerous settings, and prompt fixes are crucial to avoid expensive operational delays; yet, evaluating the extent of cylinder damage and deciding between repair and replacement is often a complex task.
When dealing with hydraulic cylinders, the decision between repairing and replacing often depends on various factors such as the extent of the damage, cost implications, the urgency of need, and the availability of parts. In this article, I will discuss with you from the perspective of someone who has experienced them.
Assessing Hydraulic Cylinder Damage
Assessing the damage to a hydraulic cylinder is a critical step in determining whether to repair or replace it.
The first step in troubleshooting hydraulic cylinder failure is to identify the symptoms. Is the cylinder falling short of performance benchmarks, or has it ceased functioning entirely? Are there oil leaks, or is there visible damage to the cylinder? The challenge in this diagnostic process lies in the multitude of components that could be at fault, such as seals, pistons, head glands, bushings, or mounts. Moreover, external factors like contamination in the system can also impede performance and lead to failure. To get to the root of the issue, one should start by taking apart the hydraulic cylinder for a comprehensive inspection of each individual component. After this thorough analysis, a decision can be made about whether to repair or replace the hydraulic cylinder.
The next consideration is the location and severity of the damage, which could influence whether it’s more cost-effective to opt for a complete replacement of the hydraulic cylinder assembly.Generally, if the damage is confined to components like the seals, head glands, pistons, bushings, or mounts, economical repair is often feasible.
However, if the damage necessitates the replacement of key assemblies like the rod or barrel, particularly in smaller cylinders produced on a large scale, the unit is likely to be deemed beyond economical repair.
Here’s how you can evaluate the condition of a hydraulic cylinder:
1.Visual Inspection
External Leaks: Check for any fluid leaking around the seals, which may indicate seal failure.
Physical Damage: Inspect for dents, cracks, or other visible damage to the barrel or rod.
Attachments and Fittings: Examine all welded or bolted connections to ensure they are secure.
2.Operational Test
Performance: Run the cylinder through its full operational range and observe any lag, juddering, or inefficient movement.
Noise: Listen for unusual sounds such as grinding or squealing, which can indicate internal damage.
3.Disassembly and Internal Inspection (Done by Professionals)
Seal Condition: Worn or damaged seals are a common issue and can often be easily replaced.
Rod Surface: Look for any scratches, pitting, or signs of corrosion.
Barrel Surface: Inspect the internal surface of the barrel for scoring or uneven wear.
Bushings and Bearings: These should be in good condition to ensure smooth operation.
4.Technical Tests
Pressure Test: A hydraulic pressure test can indicate the efficiency of the cylinder.
Tolerance Test: Measures the wear and tear of internal components against manufacturers’ guidelines.
5.Evaluation
After the assessment, you can categorize the damage as:
Minor Damage: Issues like seal leaks, slight surface imperfections.
- Suggested Action: Repair
Moderate Damage: Scoring, light corrosion, minor internal component wear.
- Suggested Action: Depending on the overall cylinder condition, either repair or replace.
Major Damage: Cracked barrel, bent rod, extensive internal wear.
- Suggested Action: Replace
Searching for Oil Leaks in Your Hydraulic Cylinder
Oil leaks in hydraulic cylinders are a common issue and can cause several problems such as reduced efficiency, increased wear and tear, and environmental concerns.
Preliminary Checks
The first step is to visually inspect the cylinder, particularly around the seals, rod, and ports. Freshly leaked oil will look clean and may accumulate around these areas. Second, Clean the cylinder and its surrounding components with a cloth to remove existing oil and dirt.
Detailed Inspection
Apply pressure to the hydraulic system while the cylinder is in a static state. Look for signs of leakage around the seals, piston rod, and connections.
Dynamic Test
Run the cylinder through its full range of motion. Keep an eye on all potential leak points such as seals, ports, and weld seams.
Environmental Conditions
Note that temperature variations can affect seal performance. Check the cylinder in both hot and cold conditions if possible. High moisture levels can also impact seal integrity.
Take into account the Downtime Associated with Hydraulic Cylinder Repairs
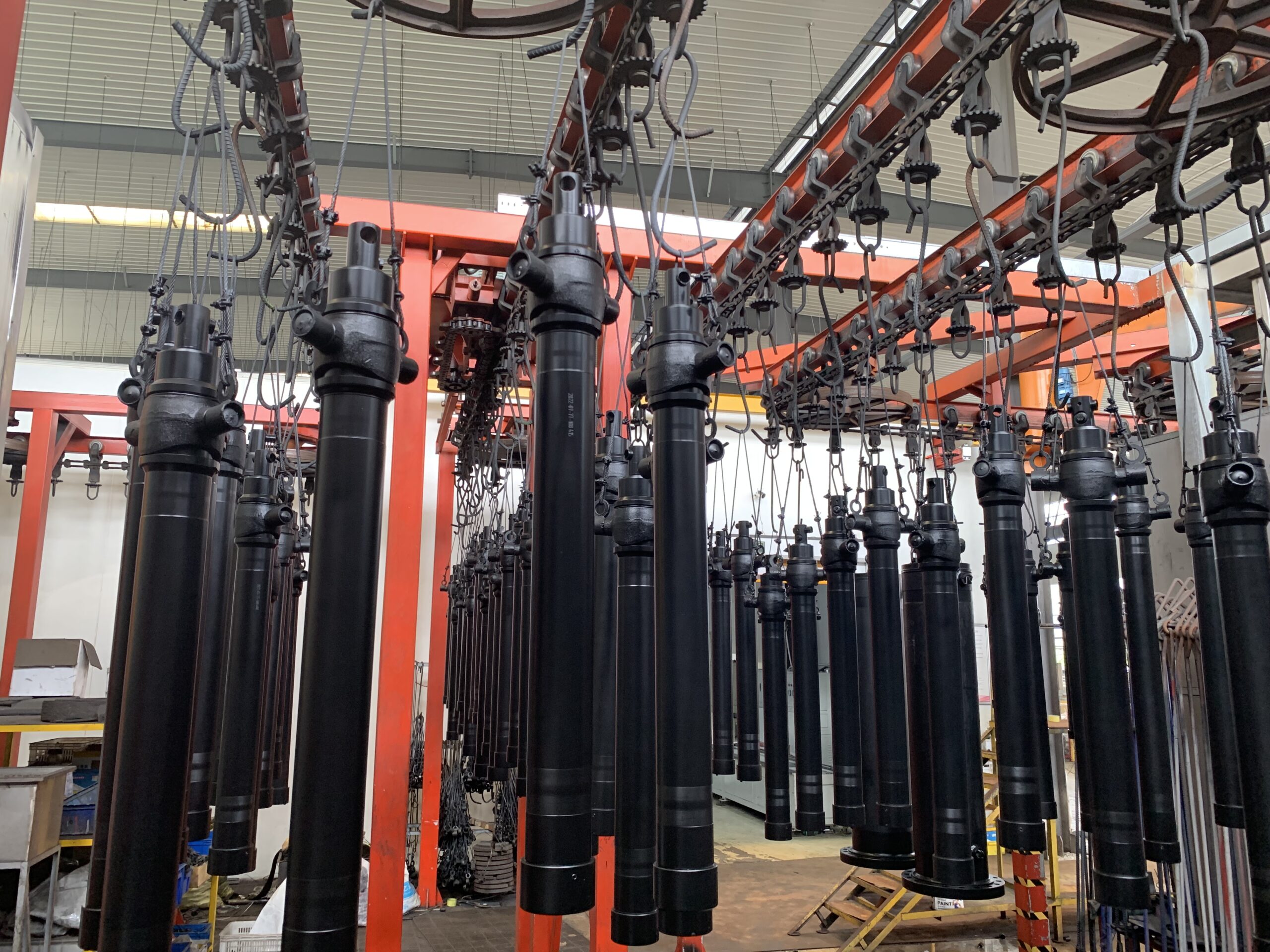
Downtime is a critical factor when considering hydraulic cylinder repairs, especially in intricate assemblies. The period during which machinery or equipment is unavailable can have a significant impact on operational efficiency, labor costs, and overall productivity. Here is a detailed explanation of various factors that contribute to downtime:
1. Factors Contributing to Downtime
Diagnostic Time: Before starting repairs, a thorough diagnosis of the problem is essential. This period can vary depending on the complexity of the issue.
Availability of Parts: If specific components need to be replaced, the lead time for acquiring these parts can extend downtime. Custom parts may take even longer to procure.
Complexity of Repairs: Some repairs may be straightforward, like replacing a seal, while others may require disassembling an intricate hydraulic assembly. More complex repairs naturally entail longer downtimes.
Technician Skill Level: The expertise of the maintenance team can significantly affect repair speed. Skilled technicians can diagnose and repair issues faster than less experienced staff.
Testing: Post-repair, the cylinder and any associated machinery need to be tested to ensure they function correctly, adding to the downtime.
2. Strategies to Minimize Downtime
Preventive Maintenance: Regular inspections and minor corrections can prevent major failures, reducing unscheduled downtimes.
Stock Critical Parts: Keeping a stock of frequently failing or crucial components can significantly cut down lead time for parts.
Skilled Labor: Invest in training for maintenance staff to enable quick and accurate repairs.
Effective Planning: Schedule repairs during non-peak hours or during planned maintenance windows to reduce the impact of downtime.
Use of Technology: Employ diagnostic tools and software to speed up the identification of issues.
In Summary
Deciding between repairing and replacing hydraulic cylinders involves considering various factors such as the extent and location of the damage, cost-effectiveness, and whether the unit is a part of a larger or more complex assembly. Repair is often feasible for minor damages to seals, pistons, or bushings, while replacement may be the better option for more severe issues or for smaller, high-volume assemblies.
Recent Posts
Share This Story, Choose Your Platform.
Leave A Comment
Your email address will not be published. Required fields are marked *