Latest News
The latest and greatest project news
How To Repair a Hydraulic Cylinder?
Hydraulic cylinders play a pivotal role in many industries, such as mobile machinery, Construction machinery etc, ensuring seamless operation and optimal performance of machinery. As the CEO of HUANUO Hydraulic, a leading manufacturer in China, I’ve seen first-hand the detrimental impacts a malfunctioning cylinder can have on operations. But what happens when they fail?
Often, the solution lies in a timely and efficient repair. But, how do you go about it?
Table of Contents
Why Is Proper Hydraulic Cylinder Maintenance Crucial?
You know, hydraulic cylinders are the lifeline of many machines. They provide the necessary force to make machinery move. A poorly maintained or damaged cylinder can lead to operational inefficiencies and increased costs. Moreover, regular checks and maintenance can significantly extend the life of your hydraulic cylinders.
What Are the Common Issues with Hydraulic Cylinders?
Here I will list several problems that can afflict hydraulic cylinders, including leakages, broken seals, damaged barrels, burr etc. Leakages are the most common, where the fluid seeps out, affecting the pressure and consequently the performance. Bent rods, often due to operational mishaps or overload, can also hamper the cylinder’s function. Internal issues like worn seals or damaged barrels can be more intricate, requiring a keen eye and expertise to diagnose.
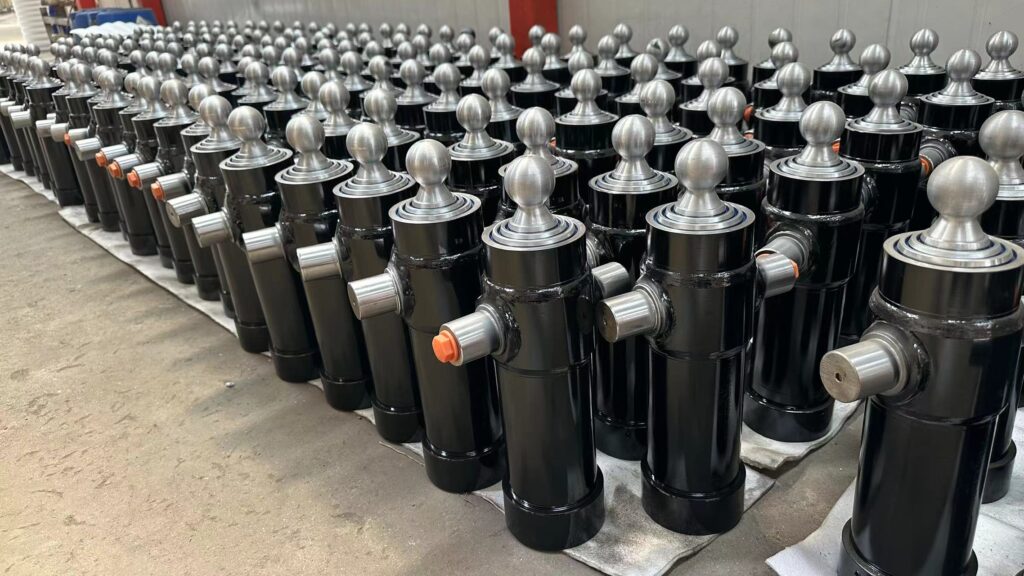
What's the Repair Process?
Once you’ve identified the issue, it’s time to roll up your sleeves. For external issues like bent rods, a replacement might be the quickest solution. For internal problems, disassemble the cylinder. Replace worn seals, and if the barrel is damaged, consider honing or reconditioning. Always ensure you have the right tools and replacement parts at hand. Remember, using quality parts, ensures longevity and optimal performance.
Different repair solution for diverse types cylinders
Various cylinder designs exist, and the approach to mending them varies based on their specific design. Predominantly, cylinders are categorized into wire ring types or threaded head types. It’s worth noting that for threaded head cylinders, there might either be a set screw or a securing ring present. It’s essential during the restoration procedure to ensure that every component undergoes a thorough cleaning using a solvent derived from petroleum. After cleaning, they should be dried using compressed air. Prior to their reassembly, it’s crucial to apply a layer of hydraulic fluid to these components.
Preparing before repairing
The initial step in getting a hydraulic cylinder ready for disassembly is to thoroughly cleanse the device. This ensures that impurities like dirt, lubricants, and other debris don’t invade the cylinder’s internal components. It’s crucial to remember that a hygienic environment is optimal for carrying out repairs. Although there might be instances where urgent fixes are required on-site, it’s always best to conduct regular maintenance and repair tasks in a location devoid of contaminants like dust and humidity.
After ensuring the device is spick and span, it’s time to detach the hoses. Ensure both the cylinder ports and the hoses are firmly sealed to prevent leakage. Subsequently, the cylinder ports can be unsealed, permitting the hydraulic liquid to be emptied out.
Hydraulic Cylinder Diagnosis
Diagnosis is a paramount initial step when addressing any concerns with a hydraulic cylinder. Before making any attempts to repair or replace parts, understanding the root of the problem is essential. The process starts with a thorough visual inspection. By closely observing the exterior of the cylinder, one can identify any noticeable damage such as dents, rust, or external leaks. Particular attention should be paid to the seals and the rod, as these are common areas where issues manifest.
Leaks, a frequent issue with hydraulic cylinders, can often be spotted as wet patches or drips around the seals. However, not all leaks are immediately visible. Some might be minor, requiring the cylinder to be under operation to be noticed. In such cases, a paper or cloth can be run along the seals to check for wetness, indicating a slow leak. Another telltale sign of internal problems is the discoloration of the hydraulic fluid, which can hint at contamination or overheating.
A bent rod, another common problem, can usually be spotted visually, but sometimes the bend is subtle. Rolling the rod on a flat surface can help determine if it’s perfectly straight. Any wobbling indicates a bend. Similarly, scratches or scuffs on the rod’s surface can lead to seal damage over time and need to be addressed.
Beyond the visual inspection, using tools can aid in the diagnostic process. Pressure gauges, for instance, are invaluable. By connecting a gauge to the hydraulic system, one can measure the operating pressure. If the observed pressure deviates from the expected range, it’s a clear sign of internal issues, possibly due to worn seals or damaged components.
Another useful diagnostic tool is the hydraulic fluid itself. Draining a small sample and examining it can provide a wealth of information. If the fluid appears cloudy, it may indicate the presence of water or other contaminants. Metal shavings in the fluid are a grave concern, signaling internal component wear or damage.
In essence, diagnosing issues in a hydraulic cylinder is a blend of observational skills and the judicious use of tools. It’s a systematic approach where each sign, be it a minor leak or a pressure deviation, offers a clue to the underlying problem. Proper diagnosis not only guides the subsequent repair process but also ensures that the root issue is addressed, preventing future complications.
Disassembling a Cylinder
Before even touching the hydraulic cylinder, one must ensure complete safety. This means deactivating the hydraulic system to prevent any unintentional activations, which can lead to accidents. Wearing the right protective gear, including gloves and safety goggles, is non-negotiable, as these prevent injuries from hydraulic fluid splashes or sudden releases of pressure.
The first actual step in the disassembly is depressurizing the hydraulic cylinder. This is typically achieved by slowly releasing any residual pressure. One can do this by gently loosening a bleed valve or methodically detaching the hydraulic lines. This step is crucial as it ensures that the cylinder can be handled without the risk of a sudden release of high-pressure fluid.
Once you’re certain that the cylinder is fully depressurized, it should be positioned horizontally on a sturdy workbench or a holding fixture. This positioning provides stability, ensuring the cylinder doesn’t roll or shift during the disassembly, which can cause damage or injury. With the cylinder stable, the next step is to address the end caps. These caps are typically held in place either by bolts or by being threaded directly onto the cylinder. If they’re bolted on, the right-sized wrench is used to remove these bolts. In cases where the end caps are threaded onto the cylinder, they’ll need to be carefully unthreaded, possibly requiring a specialized tool or wrench.
With the end caps successfully removed, one can now access the rod assembly. This assembly encompasses the rod, the piston, and the associated seals. When extracting the rod assembly, it’s imperative to pull it out in a straight line. This linear movement ensures that neither the rod nor the internal surface of the barrel suffers any damage. Once the rod assembly is out, the piston, which is usually attached to the rod via a nut or bolt, needs to be detached. Using appropriate tools, this fastener is removed, allowing for the piston to be slid off the rod.
Now, with the piston removed, the focus shifts to the seals and bearings. Found within grooves on the piston and the rod’s gland, these seals and bearings are vital for the proper functioning of the hydraulic cylinder. Removing them demands care. Using a seal pick or a similar tool, these components are carefully extracted, making sure not to scratch or damage their housing or any adjacent surfaces.
As the disassembly progresses, each component, once removed, should be cleaned immediately. This cleaning, typically done with a suitable solvent, removes old hydraulic fluid, grime, or any potential contaminants. This not only aids in inspecting the parts for wear or damage but also ensures they’re ready for eventual reassembly.
In essence, the disassembly of a hydraulic cylinder, while intricate, is a systematic process. Every step, from depressurizing the cylinder to cleaning the individual components, requires diligence. Given the variations in design across different hydraulic cylinders, it’s often beneficial to have the manufacturer’s manual or guidelines on hand, ensuring that the procedure is tailored to the specific model in question. Properly executed disassembly ensures the longevity and functionality of the hydraulic cylinder once any necessary repairs or replacements are undertaken.
Internal Inspection Of Cylinder
Once the hydraulic cylinder has been safely depressurized and disassembled, the internal components become accessible for a thorough inspection. The inner surface of the barrel is the first area of focus. This surface should be smooth and devoid of any scratches, scuffs, or pitting. Any irregularities can be indicative of wear or damage and can compromise the efficiency and lifespan of the seals. A flashlight or bore scope can be utilized to illuminate and inspect the barrel’s inner walls, ensuring that even minute imperfections are detected.
Next, the piston and its associated seals command attention. The piston should be free from any signs of wear, cracks, or deformation. Its seals, vital for maintaining pressure within the cylinder, should be closely examined for any signs of wear, tearing, or deterioration. A compromised seal can lead to a loss of pressure, rendering the hydraulic cylinder inefficient or entirely non-functional. If the seals appear flattened, cracked, or have lost their elasticity, they will require replacement.
The rod, although part of the external structure, has internal components like the rod seals and wipers that need examination during this phase. These elements prevent contaminants from entering the cylinder and maintain the internal fluid’s integrity. They should be inspected for wear, damage, or any foreign debris that might compromise their function.
The hydraulic fluid itself offers insights during an internal inspection. A sample should be taken and assessed for clarity, consistency, and any signs of contamination. Cloudy fluid may indicate water contamination, while the presence of metal shavings or particles suggests internal wear or damage. The fluid’s odor can also be telling; a burnt smell is often a sign of overheating.
Lastly, any bearings, bushings, or other minor internal components should be looked over for wear, misalignment, or damage. These smaller parts, though often overlooked, play crucial roles in the smooth operation of the hydraulic cylinder.
In summary, the internal inspection of a hydraulic cylinder is a meticulous process that assesses each component’s health and functionality. From the barrel’s inner walls to the fluid itself, every element is scrutinized to ensure the equipment’s optimal performance and longevity. Proper internal inspection not only identifies current issues but can also preemptively spot potential future problems, allowing for proactive maintenance and repair.
Hydraulic Cylinder Cleaning
Once the hydraulic cylinder is disassembled and the internal components are laid out, each part should undergo a thorough cleaning. This is essential to remove old hydraulic fluid, accumulated dirt, grime, or any contaminants. An appropriate solvent or cleaner, compatible with the hydraulic system’s specifications, should be used for this purpose.
For cleaning the internal surface of the barrel and other intricate parts, a soft-bristled brush can be effective. This ensures that any stubborn deposits or contaminants are scrubbed away without causing damage to the surfaces. After cleaning, all parts should be rinsed with a clean solvent and then dried thoroughly, either air-dried or using clean, lint-free cloths. It’s essential to ensure no solvent residues remain, as these can contaminate the hydraulic fluid and affect the system’s performance.
Repair Or Replacement
With the components cleaned, a close inspection will determine if they can be repaired or if replacement is necessary.
For the piston and rod, minor scratches or dents might be rectified through machining or honing processes. However, if there’s significant wear, deformation, or deep scoring, replacement might be the more viable option.
Seals, due to their wear-prone nature, often require replacement rather than repair. Over time, they lose their elasticity or might get damaged, leading to pressure loss in the cylinder. It’s generally recommended to replace all seals during maintenance to ensure the longevity of the system, even if only one appears worn.
Bearings and bushings, if worn out or misaligned, should be replaced to ensure smooth operation. Attempting to repair these smaller components can be labor-intensive and might not offer the reliability that new parts would.
The hydraulic fluid, if found contaminated during the diagnosis phase, should be entirely replaced with fresh fluid of the appropriate grade and specification. This ensures the smooth functioning of the hydraulic system and prevents potential damage from contaminants.
In essence, cleaning is a non-negotiable step that ensures all components are free from contaminants, providing a clear view for inspection. The decision between repairing or replacing comes down to the extent of wear or damage and the cost-effectiveness of each option. While repairs can extend the life of a component, there are instances where replacement is more practical to ensure the hydraulic cylinder’s reliability and efficient operation.
Cylinder Reassembly
Once all components are cleaned and either repaired or replaced, the reassembly process begins. It’s often helpful to lay out all the parts in the order of assembly, ensuring that no component is missed or misplaced.
The first step typically involves reinstalling the piston onto the rod. The piston is slid onto the rod and then secured, usually with a nut or bolt. It’s essential to ensure that this connection is tight and secure, preventing any potential slippage during operation. Properly aligning the piston is crucial to ensure smooth movement within the barrel.
Next, the seals, both on the piston and the rod gland, need to be set in place. Using a lubricant, often the hydraulic fluid itself, helps in sliding the seals into their respective grooves without causing any damage. This lubrication ensures a smooth movement and reduces initial wear when the cylinder is put back into operation.
With the seals in place, the rod and piston assembly can be carefully slid back into the barrel. This needs to be done with caution, ensuring that the rod enters straight, without causing any damage to the seals or the inner surface of the barrel.
The end caps, which were earlier removed, are then reattached. If they are bolted, they should be secured firmly, ensuring a tight seal. In cases where the end caps are threaded, they need to be screwed back into place, ensuring they are tight and flush with the barrel’s ends.
Once the hydraulic cylinder is fully reassembled, it’s filled with hydraulic fluid. It’s vital to ensure that the fluid level is as per the manufacturer’s recommendation and that there are no air bubbles trapped within. Air bubbles can be expelled by cycling the cylinder a few times. This “bleeding” process ensures that the cylinder operates at its optimal pressure.
Lastly, a final visual inspection is conducted to ensure all components are in place, and there are no visible issues like misalignments or leaks.
Cylinder Testing
The initial phase of testing revolves around a visual and manual check. Before introducing any pressure into the system, it’s prudent to look over the entire cylinder for any obvious issues, like misaligned components or unsecured connections. Manually cycling the cylinder, if possible, can help identify any obstructions or irregularities in the movement of the piston and rod.
Once satisfied with the initial checks, the hydraulic system is then pressurized. This should be done gradually, monitoring for any unexpected behavior or leaks. A pressure gauge is attached to the hydraulic system, and as the pressure is increased, readings on the gauge are observed. The pressure should match the manufacturer’s specifications for the cylinder. Any deviations could indicate an issue, such as a damaged seal or an improperly seated component.
While the system is pressurized, the cylinder’s operation is observed. The piston and rod should move smoothly throughout their entire range of motion without any hitches or stuttering. This smooth operation indicates that the internal components, especially the seals, are functioning correctly.
Leak testing is another vital aspect. With the system pressurized, the entire cylinder is inspected for any signs of hydraulic fluid leakage. Special attention is paid to areas around the seals, connections, and end caps. Any leakage not only reduces the efficiency of the cylinder but can also be a safety hazard.
Performance testing, where the cylinder is operated under various loads and conditions, can also be conducted. This ensures that the cylinder can handle its intended tasks without any issues.
Finally, after all tests are satisfactorily completed, the hydraulic system is depressurized, and a final visual inspection is conducted. This ensures that no components were adversely affected during testing.
Final Inspection
At the outset of the final inspection, the entire hydraulic cylinder is given a comprehensive visual assessment. This involves checking the exterior for any signs of damage, misalignment, or improper assembly. All bolts, nuts, and connections should be verified to ensure they are tightened and secured correctly. This visual check aims to identify any discrepancies that might have been overlooked during the reassembly or testing phases.
Next, the hydraulic lines and connections are inspected. They should be securely attached, with no signs of leakage or damage. Ensuring that these lines are intact is crucial, as they deliver the hydraulic fluid that powers the cylinder. Any compromise in these lines can lead to inefficiencies or malfunctions.
The seals, both internal and external, warrant special attention during the final inspection. They should appear well-seated and show no signs of damage or displacement. Seals are critical to the proper functioning of a hydraulic cylinder; hence, their integrity is paramount.
Another essential aspect of the final inspection is checking the hydraulic fluid level and its clarity. The fluid should be at the recommended level, and its appearance should be free from any cloudiness or contaminants. Any discoloration or foreign particles in the fluid could indicate internal wear or contamination, which might necessitate further investigation.
Additionally, any accompanying components or accessories, like mounting brackets or sensors, should also be inspected to ensure they are correctly positioned and functional.
Once the detailed checks are complete, the hydraulic cylinder is manually cycled a few times, if possible. This manual operation serves to confirm that the movement is smooth, consistent, and free of any obstructions or hitches.
In conclusion, the final inspection of a hydraulic cylinder is a meticulous process that acts as a final quality control measure. It ensures that every component, from seals to hydraulic lines, is in optimal condition. This thorough inspection provides assurance that the hydraulic cylinder is not only functional but also meets all safety standards, ready to be put back into regular service.
By following this repair process, you can ensure that your hydraulic cylinder is restored to its optimal working condition, ensuring safety and efficiency in its operations. If you’re unsure about any step, it’s always advisable to consult a professional or expert in hydraulic systems.
How Important Is Expertise in Repair?
While some minor repairs can be DIY, expertise is crucial for complex issues. A wrongly repaired hydraulic cylinder can be a safety hazard. It’s always advisable to consult or hire professionals for repairs. At HUANUO, we offer consultation services, guiding our clients through the repair process, ensuring safety and efficiency.
Conclusion
Hydraulic cylinders are integral to operations in various industries. Ensuring their optimal performance is not just about efficient operations but also about safety. Regular maintenance, timely repairs, and seeking expertise when in doubt can save both time and money. At HUANUO, we pride ourselves on offering top-notch products and sharing our expertise, ensuring our clients get the best out of their hydraulic cylinders.
HUANUO Hydraulics
At HUANUO Hydraulics, we specialize in comprehensive hydraulic cylinder repairs. From installing fresh seals and honing tubes to polishing rods and crafting custom replacement parts, we cater to all brands with precision. Our advanced infrastructure encompasses capabilities for tube, rod, and cylinder creation, as well as expert machining and welding services. To enhance convenience for our clients, we proudly offer round-the-clock cylinder resealing and a dedicated pick-up/delivery service. If your hydraulic cylinders require professional attention, reach out to HUANUO Hydraulics for prompt, top-tier, and reliable services.
Recent Posts
Share This Story, Choose Your Platform.
Leave A Comment
Your email address will not be published. Required fields are marked *