Latest News
The latest and greatest project news
What Is a Directional Control Valve?
Hydraulics have always fascinated me. In the intricate world of hydraulics, few components command as much attention as the directional control valve. Every day, I find myself immersed in discussions with clients, partners, and my talented team about the pivotal role these valves play. But what exactly it is?
A directional control valve manages the flow path of fluid within a hydraulic system. It dictates the flow of fluid, ensuring that it moves in the right direction at the right time. Imagine a busy intersection in a city. Without traffic signals or a traffic officer, chaos would reign. Similarly, in a hydraulic system, without a DCV, fluid would flow aimlessly, rendering the system ineffective.
But how do these valves actually function? And why should businesses, particularly those in the hydraulics field, care? With this in mind, I’d like to delve deeper, sharing my insights and expertise on the subject.
Table of Contents
Decoding the Mechanics: How Does a Directional Control Valve Work?
A directional control valve works by shifting a spool to block or permit fluid flow. Think of it like a sliding door: when open, fluid can pass through freely, but when closed, the flow is halted. This simple mechanism is what allows engineers and technicians to control machinery with precision. The number of positions and pathways, often referred to as “ways”, determines the valve’s functionality.
The Basic Premise
Directional control valves (DCVs) are essential in determining the path that fluid takes within a hydraulic system. Their primary function is to allow or restrict fluid flow to different parts of the system, ensuring that machinery and equipment operate as intended. Imagine it as a series of gates or doors; the valve decides which gates to open and which to close, directing the flow of fluid accordingly.
Core Components
Every directional control valve is made up of a few key components:
Valve Body: The main casing that houses the internal parts.
Spool: A cylindrical piece that slides back and forth within the valve body. The spool’s position determines the flow path of the fluid.
Actuators: These are mechanisms that control the position of the spool. Actuators can be manual levers, electrical solenoids, pneumatic, or hydraulic pilots.
The Spool’s Role
The spool’s movement is central to a DCV’s function. As it slides within the valve body, it aligns with different ports, either opening or closing pathways for the fluid. When the spool is in its neutral position, it might block all ports, preventing fluid movement. But when actuated, it shifts to allow fluid to flow through specific paths, based on the desired operation.
Configurations and Designations

What Types of Directional Control Valves Exist?
1. Spool Valves
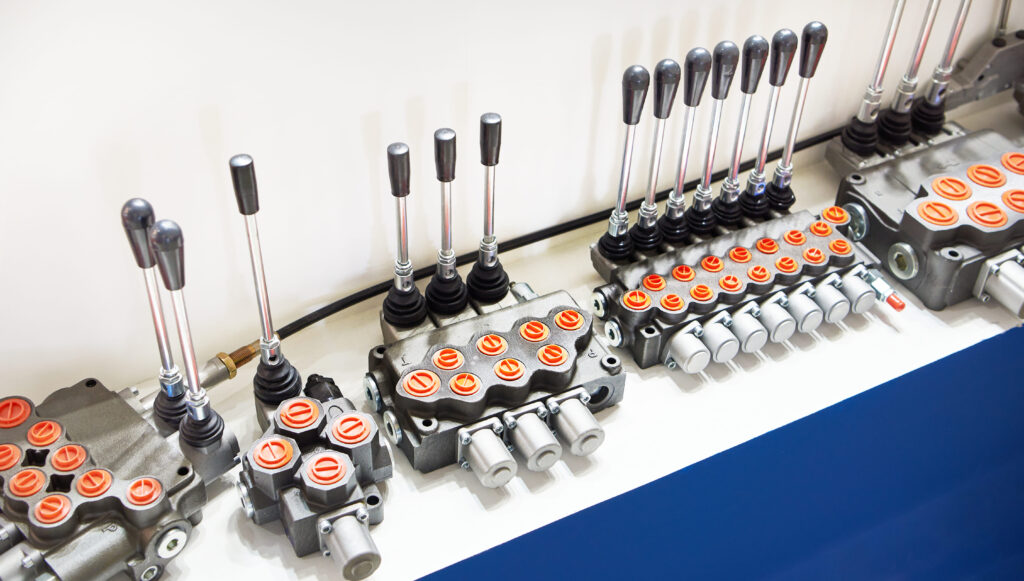

The most prevalent type, identified by its sliding spool mechanism.
Based on the Number of Positions and Ways:
- 2/2 Valve: 2 positions (open/closed) and 2 pathways (ports).
- 3/2 Valve: 3 ports and 2 positions. Commonly used for single-acting cylinders.
- 4/2 Valve: 4 ports and 2 positions. Suitable for double-acting cylinders.
- 4/3 Valve: 4 ports and 3 positions. Offers more flexibility in controlling double-acting cylinders.
- 5/2 Valve: 5 ports and 2 positions. Typically used for controlling double-acting actuators.
- 5/3 Valve: 5 ports and 3 positions. Offers more control options for double-acting actuators. function.
Based on Actuation Methods:
- Manual Spool Valves: Actuated by manual force, like a lever or push button.
- Solenoid-Actuated Spool Valves: Use an electric current to generate a magnetic field that shifts the spool.
- Pilot-Actuated Spool Valves: Use hydraulic pressure from a pilot valve to actuate the spool.
- Mechanically Actuated Spool Valves: Rely on mechanical forces, such as springs or cams, to move the spool.
- Open Center: When the spool is in its neutral position, the pump flow is connected directly to the tank, allowing fluid to flow freely.
- Closed Center: In the neutral position, all ports are blocked, stopping the fluid flow.
- Float Center (Tandem Center): The actuator ports are blocked, but the pump flow is connected directly to the tank in the neutral position.
- Regenerative Center: Connects the two actuator ports in the neutral position, allowing for faster extension or retraction of a double-acting cylinder.
Based on Flow Rate and Pressure:
- Low-Flow Spool Valves: Designed for systems with a lower flow requirement.
- High-Flow Spool Valves: Suitable for systems requiring a higher flow rate.
- Low-Pressure Spool Valves: Operate at lower pressure ratings.
- High-Pressure Spool Valves: Designed to withstand and operate at higher pressures.
Based on Construction:
- Sliding Spool: The spool slides within the sleeve or bore of the valve.
- Rotary Spool: The spool rotates to align with specific ports.
2. Rotary Valves
As the name suggests, these valves use rotation to control fluid flow, suitable for high-flow applications.
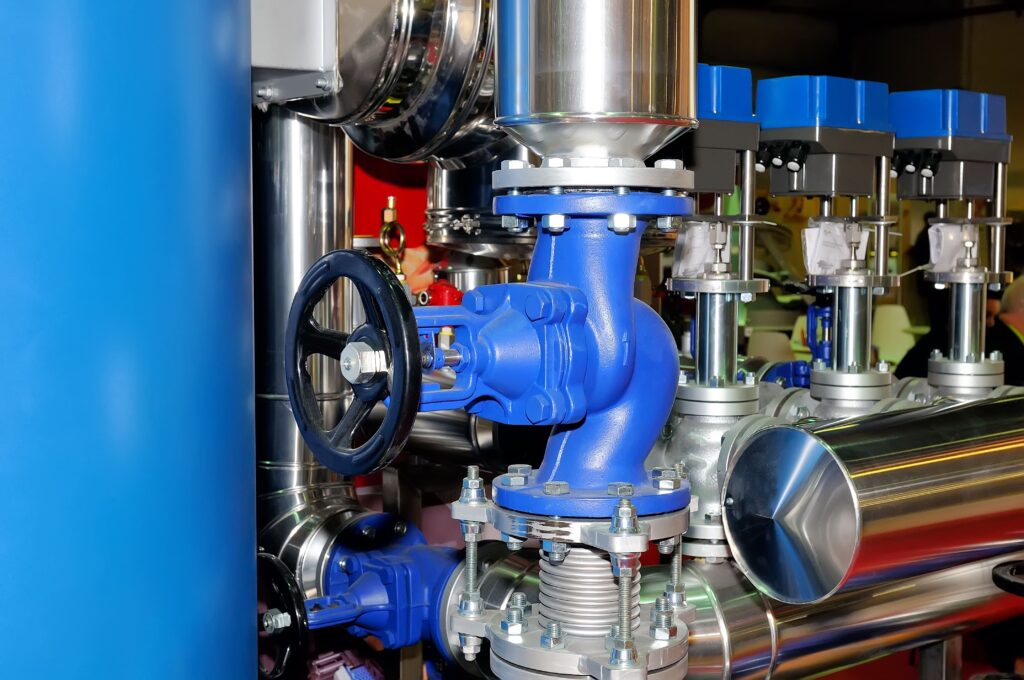
3. Poppet Valves
These utilize a piston or poppet for flow control, offering rapid response but potentially limited flow rates.

Guiding Your Choice: How to Select the Ideal Valve?
In the realm of hydraulic systems, the selection of the appropriate valve is both an art and a science. Here’s a deep dive into how to make the right choice for your hydraulic needs.
1. Understand Your Application
The first step in selecting the ideal valve is a thorough understanding of your application.
- Purpose of the Valve: Are you looking to control flow, pressure, or direction? For instance, a directional control valve would be ideal for managing the path of fluid, whereas a pressure relief valve would be suitable for maintaining a preset pressure.
- Machinery and Equipment: The type of machinery you’re operating will dictate the valve’s specifications. Mobile machinery might have different requirements compared to stationary industrial machinery.
- Operational Conditions: Consider the environment where the valve will be used. Will it be exposed to extreme temperatures, corrosive substances, or outdoor conditions?
2. Evaluate Technical Specifications
- Flow Rate: Determine the flow rate your system requires. The valve should be able to handle this flow without causing excessive pressure drops.
- Pressure Ratings: Ensure the valve can withstand the maximum pressure of your system. Remember, always choose a valve with a pressure rating higher than your system’s maximum operating pressure.
- Size and Port Configurations: The valve should fit seamlessly into your system. Consider the port sizes, types (e.g., threaded, flanged), and their configuration.
- Response Time: For applications that need rapid actuation, the valve’s response time becomes critical.
3. Consider the Actuation Method
Different applications might require different actuation methods:
- Manual: Suitable for systems where frequent adjustments aren’t necessary.
- Solenoid: Ideal for automated systems requiring electrical actuation.
- Pilot-operated: Useful for systems where a secondary hydraulic source can control the valve.
- Mechanical: Best for systems where external mechanical forces, like springs or cams, are available for valve operation.
4. Material and Construction
- Material: Depending on your working fluid and environmental conditions, select a valve material that offers the best corrosion resistance and durability. Common materials include brass, stainless steel, and plastic. Construction
- Quality: Always opt for valves that have a reputation for durability and robust construction. This is where partnering with trusted manufacturers, like HUANUO Hydraulic, becomes invaluable.
5. Cost and After-sales Support
While cost is always a factor, it should never be the sole criterion. Opt for valves that offer the best value – a balance of price, performance, and durability. Additionally, consider manufacturers that provide excellent after-sales support, ensuring prolonged service life and performance.
6. Consult with Experts
Lastly, and perhaps most importantly, consult with hydraulic system experts or engineers. Their insights, combined with your application understanding, can guide you to the perfect valve choice.
7. Customizability and Modular Designs
In response to varied industry needs, DCVs will adopt modular designs, allowing for greater customizability. Whether it’s different actuation methods, port configurations, or flow rates, these modular DCVs can be tailored to specific requirements, offering greater flexibility.
8. Integration with Digital Twins
Digital Twins, or virtual replicas of physical systems, are becoming prominent in many industries. In the realm of hydraulics, this means DCVs that can be simulated in a digital space before being deployed in the real world. This not only aids in design and testing but also in troubleshooting and training.
Applications of Directional Control Valves across Different Industry Sectors
1. Construction and Earthmoving Equipment
Excavators: DCVs help control the arm movements, bucket operation, and swiveling of the cabin.
Backhoe Loaders: The extension, retraction, and swivel of the digging arm are managed by these valves.
Bulldozers: For lifting and tilting the blade or ripper, DCVs are essential.
2. Agriculture
Tractors: Directional control valves play a role in lifting and adjusting agricultural implements attached to tractors.
Harvesters: They aid in controlling various components like the cutting and gathering mechanisms.
Sprayers: For adjusting the boom and controlling the spray nozzles, DCVs are used.
3. Manufacturing and Industrial Machinery
Assembly Lines: They ensure precise movement and positioning of parts during the assembly process.
Presses and Stamping Machines: DCVs control the descent and ascent of the pressing or stamping component.
Conveyor Systems: For start-stop operations and directional changes of conveyor belts.
4. Aerospace and Defense
Aircraft Landing Gear: DCVs manage the retraction and extension of landing gears in aircraft.
Missile Launch Systems: They play a role in adjusting missile launch angles and initiating the launch sequence.
5. Marine
Ship Rudder Control: DCVs assist in adjusting rudder angles for steering large ships.
Submersible Vehicles: For adjusting buoyancy and directional control in deep-sea exploration vehicles.
6. Mining
Drilling Rigs: DCVs manage the drilling depth and angle adjustments.
Dump Trucks: They control the lifting and tilting of the dump bed. Excavators: In mining, these machines require precise control for digging and material handling, facilitated by DCVs.
7. Energy and Power Generation
Hydroelectric Dams: DCVs control water flow through turbines, adjusting power output.
Wind Turbine Hydraulics: For adjusting blade angles and yaw mechanisms, ensuring optimal wind capture.
The Horizon Ahead: What's the Future of Directional Control Valves (DCVs)?
In the hydraulic universe, directional control valves (DCVs) have always held a pivotal role, directing fluid flow and ensuring efficient machinery operation. However, as with all technologies, they are not immune to the winds of change. The future of DCVs is on the cusp of significant transformation, driven by technological advancements, industry demands, and evolving global scenarios. Let’s explore what the future holds for these vital components.
1. Integration with Advanced Sensor Technology
Modern DCVs are increasingly integrating with advanced sensors that can provide real-time feedback on valve position, flow rate, and pressure. This enables more precise control and monitoring, reducing system inefficiencies and ensuring optimal performance. For instance, sensors can immediately detect any irregularities or blockages, allowing for swift corrective actions.
2. Miniaturization and Compact Designs
As machinery and equipment trend towards compactness without compromising on power, DCVs are also undergoing miniaturization. Future DCVs will be smaller, lighter, yet equally (if not more) efficient. This is especially relevant for applications where space is at a premium, such as in aerospace or medical devices.
3. Enhanced Energy Efficiency
With increasing emphasis on sustainability and energy conservation, the next generation of DCVs will be designed for maximum energy efficiency. By reducing energy consumption, not only do they contribute to environmental sustainability, but they also result in cost savings for operators.
4. Smart Valves: IoT and Connectivity
The Internet of Things (IoT) is making inroads into the world of hydraulics. Future DCVs will have enhanced connectivity features, allowing them to be part of a networked system. This paves the way for predictive maintenance, where potential issues can be identified and rectified even before they manifest, reducing downtime and maintenance costs.
5. Adaptive and Self-learning Valves
With the integration of Artificial Intelligence (AI), future DCVs will be adaptive and self-learning. They will be able to adjust their operations based on the data they collect, optimizing performance based on specific conditions and requirements.
6. Enhanced Durability with New Materials
Research into new materials promises DCVs that are more resistant to wear and tear, corrosion, and high pressures. This means longer lifespans, reduced maintenance, and better performance even under extreme conditions.
7. Customizability and Modular Designs
In response to varied industry needs, DCVs will adopt modular designs, allowing for greater customizability. Whether it’s different actuation methods, port configurations, or flow rates, these modular DCVs can be tailored to specific requirements, offering greater flexibility.
8. Integration with Digital Twins
Digital Twins, or virtual replicas of physical systems, are becoming prominent in many industries. In the realm of hydraulics, this means DCVs that can be simulated in a digital space before being deployed in the real world. This not only aids in design and testing but also in troubleshooting and training.
Conclusion
In the realm of hydraulics, the directional control valve stands as a pivotal component, driving efficiency, precision, and operational excellence. As the manufacturer and user of it, I can attest to its significance, not just in terms of functionality but in shaping the future of hydraulic technology. For those in the industry, understanding and investing in a high-quality valve is not just a choice; it’s an imperative.
Recent Posts
Share This Story, Choose Your Platform.
Leave A Comment
Your email address will not be published. Required fields are marked *